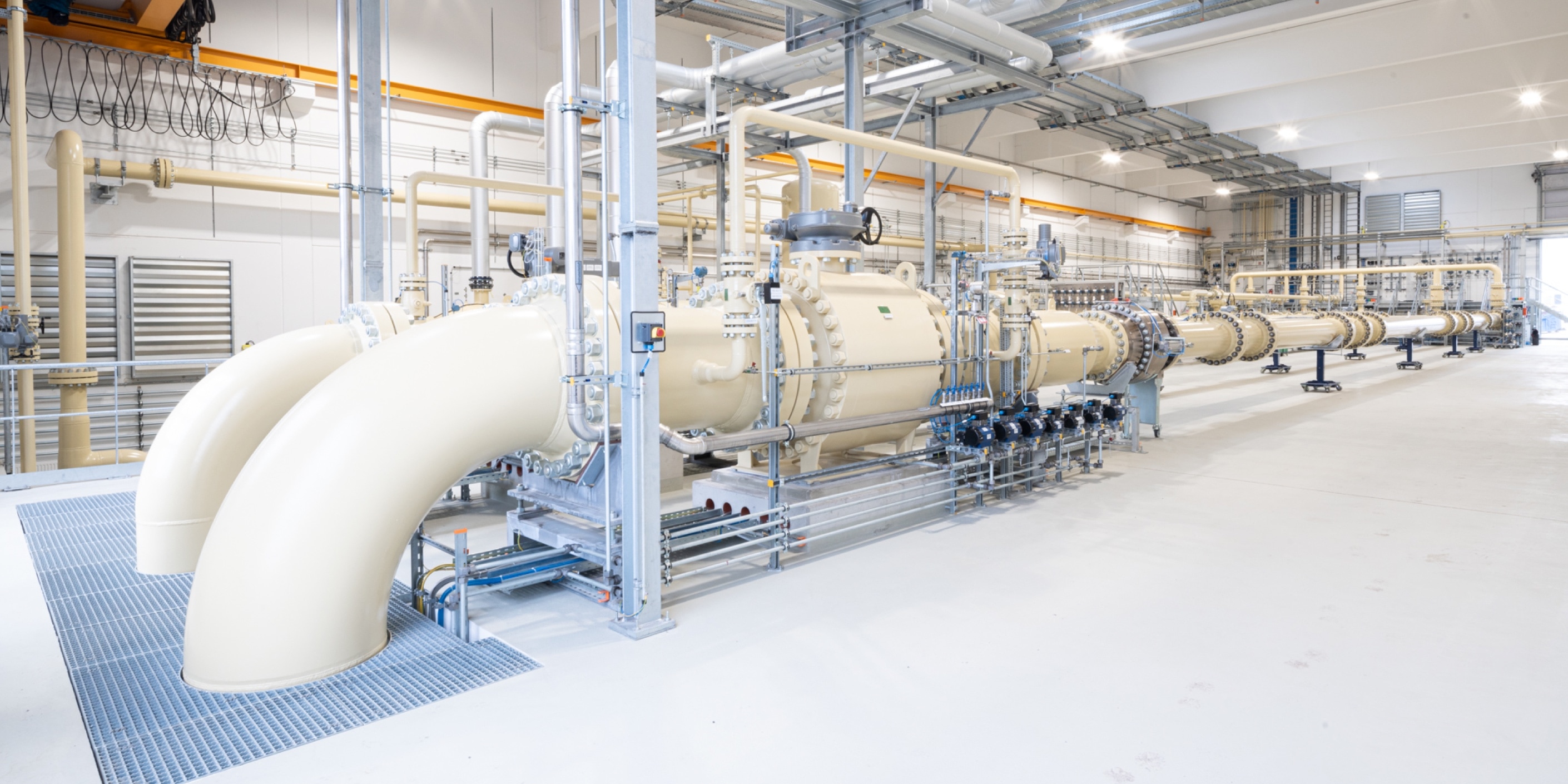
The Closed Loop pigsar™
Higher pressure. More flow. Bigger Loop.
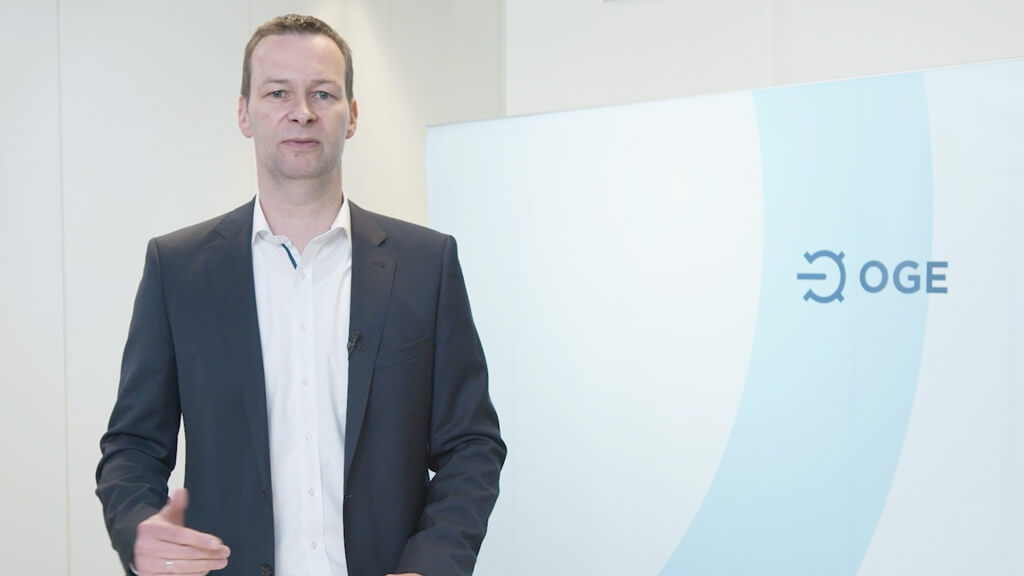
Precision, commitment and heart and soul - Video message from the OGE
On behalf of OGE, Dr Thomas Hüwener congratulates on the successful commissioning of the Closed Loop pigsar.
He thanks the employees of all the companies involved for their high level of commitment and passion - without them, such projects could not be realised so successfully.
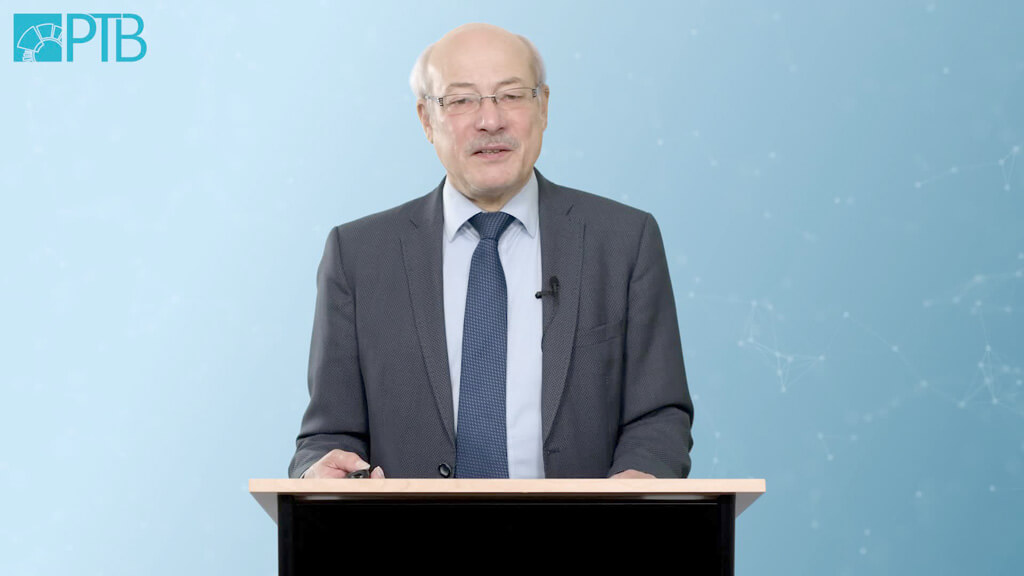
Message of congratulations from the PTB
The National Metrology Institute of Germany, represented by its President Prof. Dr. Joachim H. Ullrich, congratulates on the commissioning of the Closed Loop pigsar and highlights its importance for the future of high pressure natural gas measurement in Germany.
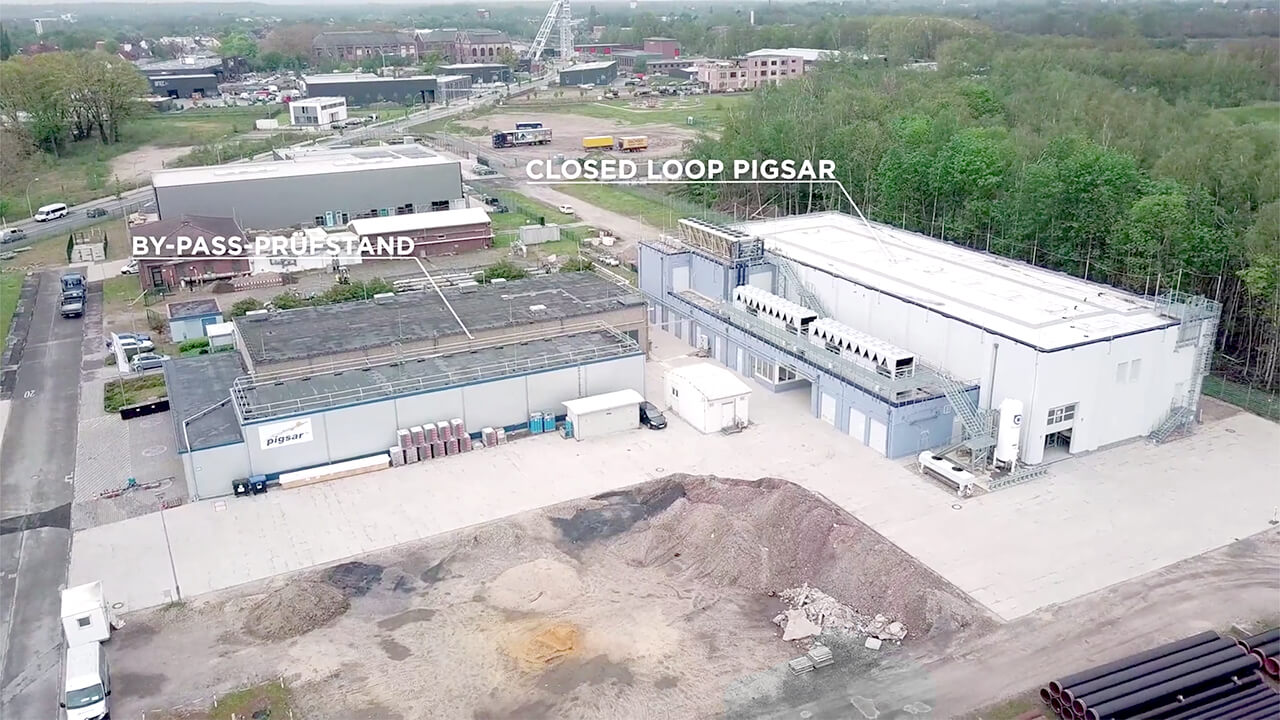
pigsar™ – An Insight
An insight into the work of the pigsar facility in Dorsten and into the significant expansion, the new Closed Loop pigsar.
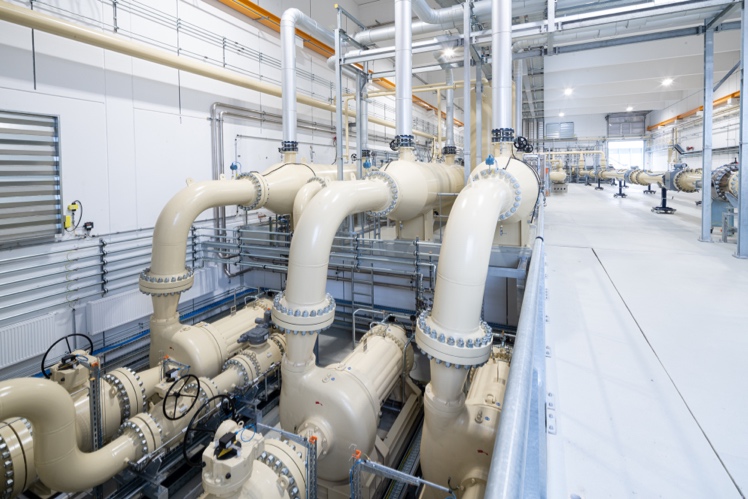
Would you like to find out more?
We would like to explain all details to you in online seminars and looking forward to answer your questions. If you are interested, just send a message to info@ with your contact details! We will send you an invitation and the login details by email. pigsar.de
Highlights
The new CLP allows customer meter runs with a length of up to 37 m to be tested.
The CLP is designed for ultrasonic flowmeters (with long upstream straight lengths, and the configuration to be calibrated can include up to 2 flow straighteners).
The pressure range has been increased to 8 - 65 bar.
Flow rates can be as high as 30,000 m³/h (under operating conditions), and the meters can have nominal diameters of up to DN500 (and more).
Four meters (connected in series) can be tested simultaneously.
The CLP has been derived from the national standard of the Federal Institute of Physics and Metrology (PTB) and therefore offers the best possible measurement accuracy.
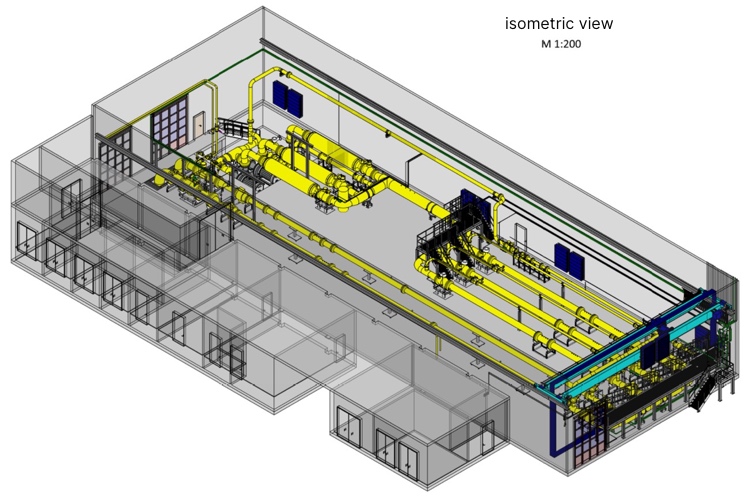
Isometric representation of the new test building with the adjoining buildings
Technical data
The key technical data of the new CLP and the existing bypass facility are summarised in Table 1. The maximum possible flow rate under operating conditions depends on the differential pressure in the test meter run as well as the test pressure and can be up to 30,000 m³/h in the medium pressure range.
New Closed Loop pigsar™ | Current pigsar™ facility | |
Flow rate | 40 - 30,000 m³/h | 3 - 6,500 m³/h |
Absolute test pressure | 9 - 66 bar | 17 - 51 bar |
Meter size | DN200 - DN600 (8“ - 24“) | DN25 - DN400 (1“ - 16“) |
Flange sizes and pressures | ANSI 150 - 1500 PN 16 - 64 | ANSI 150 - 1500 PN 16 - 64 |
Length of meter run | approx. 37 m | 8 - 22 m |
Medium | Natural gas | Natural gas |
CMC uncertainty (k=2) | 0.137 % - 0.193 % | 0.13 % - 0.16 % |
Reference turbine flow meters | 3x DN150 / G400 (G1000) 3x DN500 / G6500 | 4x DN100 / G250 4x DN200 / G1000 1x DN80 / G160 |
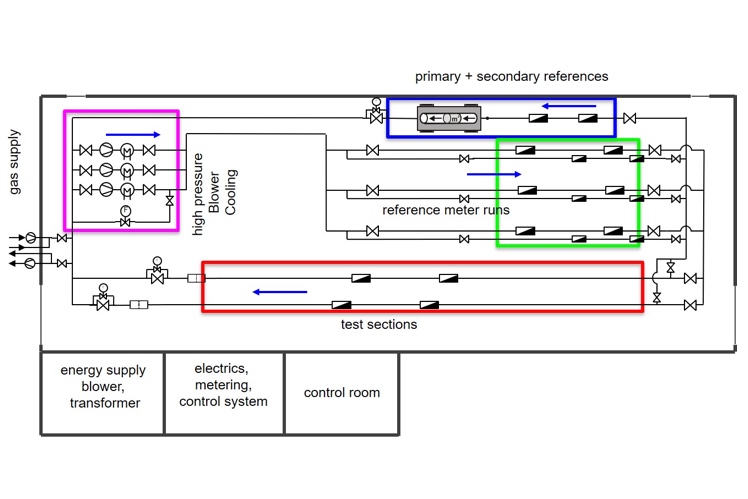
Schematic diagram of the Closed Loop pigsar™
CLP design
Looking downstream, the CLP consists of the following key components (see schematic diagram):
- The CLP is filled and depressurised in a pressure range of 17 - 50 bar from the high-pressure gas transmission network. Two high-pressure compressors are provided to raise the CLP pressure to 66 bar or reduce it to 2 bar, which minimises gas losses.
- Three parallel high-pressure blowers, each with a maximum output of approx. 950 kW, generate a continuous flow. The flow rate is controlled by the blower motors’ frequency converters. Smaller flows are controlled using bypass lines. The blowers can raise the pressure to almost 4 bar. Heat exchangers are provided to remove the heat introduced by the blower, thereby providing optimum temperature stability.
- The reference value is determined by means of 6 runs fitted with a measurement standard, see Table 1. The standards are designed to allow a total volumetirc flow rate of up to 36,000 m³/h to be measured. Turbine flow meters are used as standard meters, while ultrasonic flowmeters are installed upstream as reference standards.
- The two test runs have a diameter of DN500 and DN400, but larger or smaller meters can be fitted too. As with the existing pigsar™ system, the test meter runs can also be fed via smaller pipe connections to reduce the so-called line-pack effect when flow rates are low. The length of the test meter runs is 37 m (max.), which allows large ultrasonic flowmeters with sufficiently long upstream straight lengths to be tested even if connected in series.
- There is also a third DN200/DN250 meter run for new primary and secondary standards from PTB. These meters are used to calibrate and regularly check the working standards.
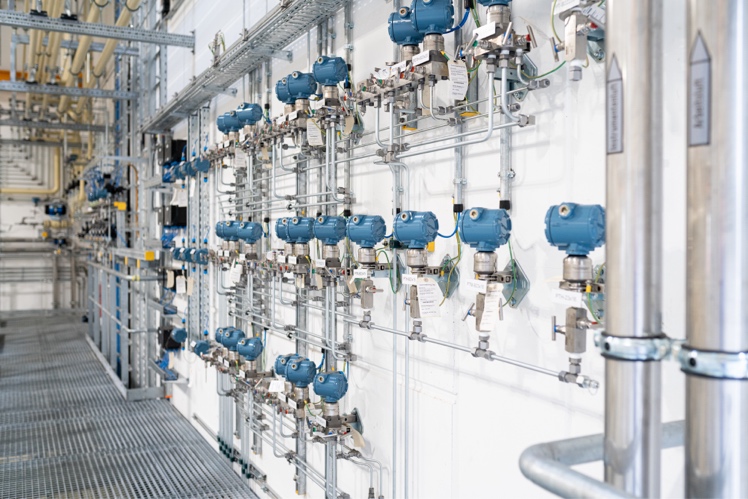
Measurement uncertainty / traceability
pigsar™ plays a key role for the realisation and dissemination of the national cubic metre for high-pressure natural gas flow measurement and the harmonised European cubic metre of natural gas. All national and some international test facilities are traceable to the German cubic metre as determined by pigsar™.
The new CLP benefits from this traceability in that the CLP standards are directly calibrated for pressures of 16 to 50 bar and up to 6500 m³/h using the existing, highly accurate calibration chain. Transfer meters are used for flow rates of up to 30,000 m³/h and other pressure ranges, which ensures optimum measurement accuracy.
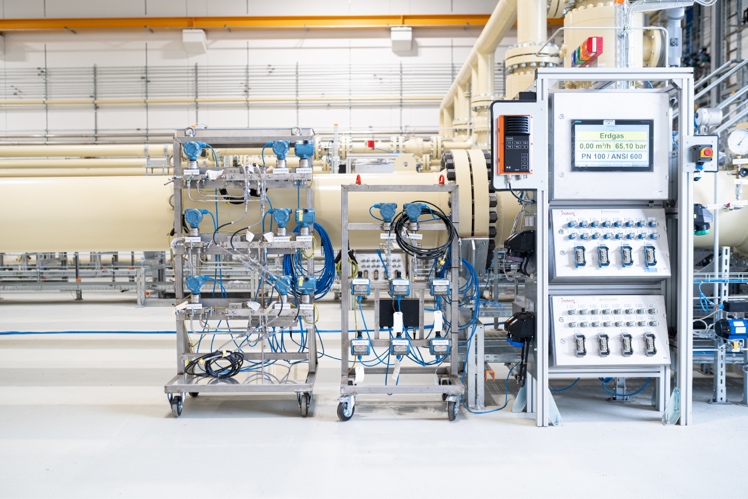
Future developments concerning the traceability chain
The implementation of the harmonised European reference value has shown that it is possible to reduce the uncertainty of measurement by linking different independent national calibration chains. A necessary prerequisite is that the influence of all stochastic uncertainty contributions is smaller than the influence of the traceability chain’s uncertainty, as in the case of the traceability chains involved in the harmonisation.
One of the research projects underway at PTB is looking into copying the procedure for the harmonised reference value at national level by developing additional, independent traceability chains. The aim is to improve the measurement uncertainty of the existing pigsar™ facility and the new CLP. For this purpose, PTB are currently developing two independent traceability chains:
- One new, independent traceability chain relies on critical nozzles. The uncertainty achieved here by geometrical measurement, theoretical approaches and calibrations with standards at PTB (up to 16 bar air) is as low as ≤ 0.15 %.
- The other development is the new PTB HP Comparator. Unlike the piston prover, this design is based on a piston/cylinder system with an actively driven piston. PTB are currently testing a smaller-scale prototype. The aim here is to provide a new primary standard for the CLP for the 40 - 1600 m³/h flow range with a measurement uncertainty of 0.1 %.
These two new calibration chains can be combined with the current calibration chain by using the transfer package. In this combination, the measurement uncertainty of this transfer package can be as low as 0.075 %, which will significantly reduce the measurement uncertainty (CMC value) for pigsar™.